-
MC Know-how for Stuttgart 21 - the Albvorland Tunnel
The Albvorland Tunnelis one of several major tunnel projects of Stuttgart 21, in which different MC technologies and product systems were used successfully.
Effective manhole rehabilitation in Halstenbeck, Germany
Halstenbeck - Germany
The municipal authorities of Halstenbeck, a town near Hamburg, had 75 sewerage-access manholes rehabilitated using MRT (Manhole Rehabilitation Technology) towards the end of 2019. This involved applying a combination of ombran MHP-SP special mortar and the hybrid silicate coating ombran FT from MC-Bauchemie, which offers durable resistance to biogenic sulphuric acid.
In addition to the usual age-related weathering, the up to 4.90 m deep, size DN 1000 concrete and masonry manholes in Halstenbeck had also suffered biogenic sulphuric acid corrosion (BSAC). The Pinneberg branch of consultant engineers d+p danekamp und partner was commissioned to plan the necessary refurbishment measures, which were then carried out by WEHE GmbH & Co. KG, a specialist contractor from Neuenkirchen-Vorden. In order to achieve a lasting rehabilitation result, the planners and contractor opted for the automated shaft rehabilitation technology developed by HDT GmbH and MC-Bauchemie using the MRT method and optimally matched special coatings from MC.
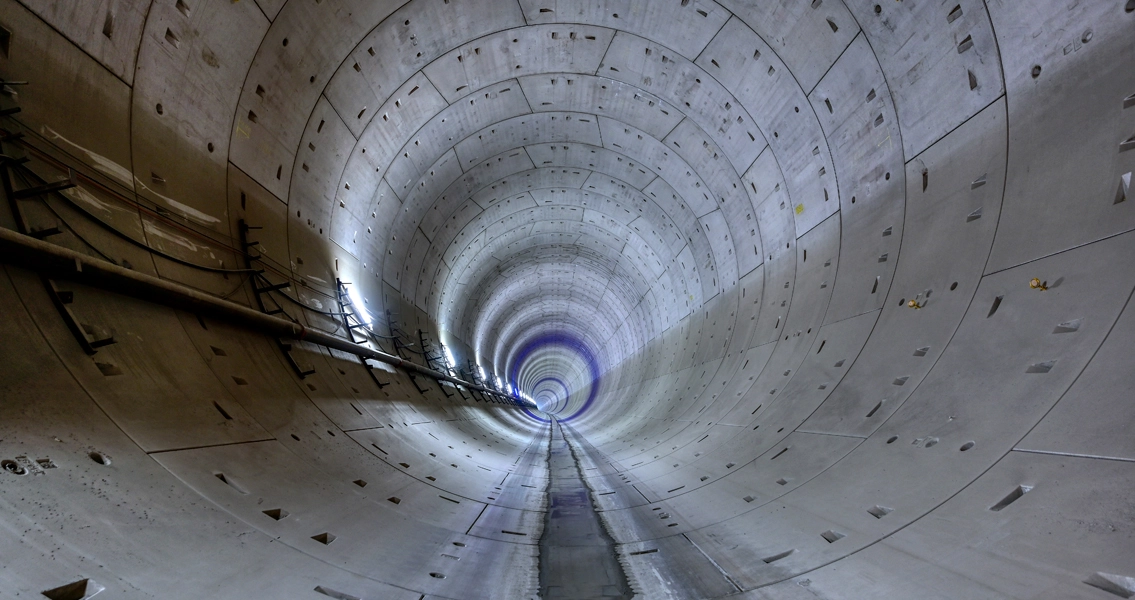
© MC-Bauchemie 2025
High efficacy thanks to the MRT truck
The refurb measures in Halstenbeck were particularly effective thanks to the use of an MRT Truck. This comes with all the requisite MRT components and supplementary rehabilitation equipment, and can be used for both round and angular manhole structures of concrete or masonry down to a depth of 10 m.
With this technology, the need for operatives to enter the manhole is reduced to a minimum, with all the technically difficult and dangerous work on the vertical shaft walls being carried out automatically.
Reprofiling with special mortar
As the first stage in the process, the cleaning and preparation of the manhole walls in Halstenbeck was carried out by the MRT blasting unit and a hand lance to control a high pressure water jet at approx. 500 bar carrying granulate as the abrasive. After successful testing of the surface tensile strength, the berms were coated with the special mortar ombran MHP 15. The following day and with the drain still operational, the channel was fully covered and the MRT spinning unit was lowered into the manhole shaft so as to automatically apply its first coating of ombran MHP-SP with a layer thickness of 15 mm. Both mortars in the ombran system are polymer-modified, highly resistant to chemical – and particularly – sulphate attack and classified according to DIN 19573 as a WW coating and grouting mortar per B1 – XWW3.
Durable protection against BSAC with ombran FT
Long-lasting BSAC protection was provided by the hybrid silicate resin ombran FT, which is optimally matched to the repair coat of ombran MHP mortar. The ombran FT coat was applied with the automatic HS coating head in a layer thickness of 4 mm. The air humidity from the flowing waste water caused by ongoing sewerage operations actually helped to cure the BSAC-protective coating. Due to its extremely dense matrix, ombran FT is highly resistant to mechanical stress and will readily withstand even heavy chemical attack. It also offers a high water vapour diffusion capability, thus effectively preventing osmotically induced bubble formation.
In Halstenbeck, the campaign was managed so that 4 to 10 manholes per road could be rehabilitated in one day using the MRT method. In addition to the time and cost savings engendered, the process ensured high, fully reproducible rehabilitation quality levels and significantly improved occupational safety compared to conventional manual application.
-
Name
Effective manhole rehabilitation in Halstenbeck, Germany
-
Country
Halstenbeck - Germany, 2021
-
Categories
-
Nyheder
Klik her for at gå til vores nyhedssektion.
-
MC-Pedia
I vores MC-Pedia finder du tekniske artikler om forskellige emner udelukkende skrevet af vores specialister.
-
Magasin
Få vores seneste numre af vores kunde- og medarbejdermagasin MC aktiv.
-
Downloads
Du kan se alle relevante datablade for vores produkter samt brochurer om vores firma, ekspertise og produktkategorier her.
-
Referencer
Klik her for at komme til vores bibliotek med referenceprojekter til alle typer applikationer.
-
Karrierer
Klik her for at gå til MC Career.
-
Kontakt
Klik her for at gå til vores kontaktsektion.